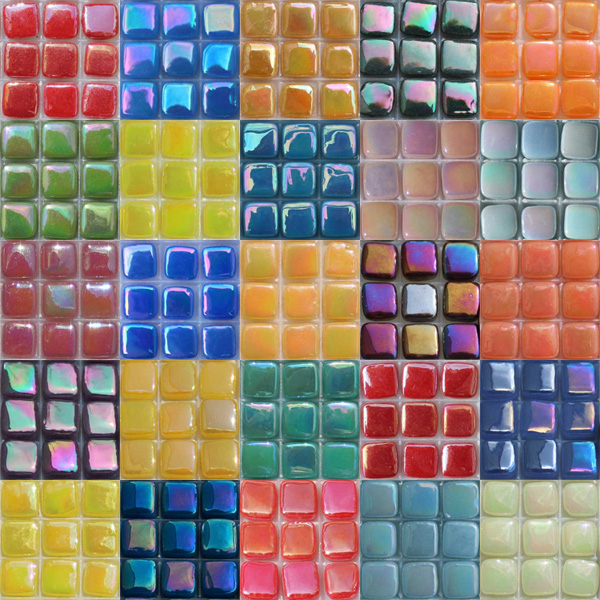
5/16 inch (8mm) Iridescent Glass Mosaic Tiles by Elementile are iridized versions of the standard gloss-finish product, which we also sell. The iridescence is a surface finish created by firing metal oxides onto the surface of the glass, so it could be abraded over time by foot traffic. Note that the iridescence is deliberately mild instead of heavily applied so that the underlying colors are still visible. Like the regular 8mm, these are sold loose by the 1/4 pound (approximately 175+ pieces), which covers 0.14 square feet with a standard grout gap of 1/32 inch. Mounting grids are available. Made from recycled glass.
Elementile 8mm Iridescent Glass Mosaic Tiles
- tile size: 5/16 inch (8mm)
- thickness: 1/8 nominal (4mm)
- sales unit: 1/4 pound (approximately 175+ pieces)
- material: glass
- variety: recycled
- finish: iridescent
- pigments: colorfast, UV resistant
- durability: frost-proof, impervious to liquid
- usage: suitable for indoor and outdoor use
Coverage
A 1/4 bag of 175 loose tiles will cover 0.14 sq ft. with a grout spacing of about 1/32 inch. To cover 1 square foot with a standard grout spacing of about 1/32 inch, you would need 1225 tiles or seven bags, but for large area coverage, order a little extra in case the tile is running incrementally thicker/heavier than normal, which could cause the piece count to run under 175. Use our tile estimator to calculate how much you need for your project.
Note that dry indoor mosaics do not have to be grouted (and thus you can simply mount the tiles tightly together), but outdoor and wet mosaics must have grout to prevent water from penetrating behind the tiles. The best way to ensure that the gaps between the tiles is to leave a 1/32-inch gap instead of pressing them tightly together, and this point seems counter intuitive to some people. Consider this: you can never mount tile so closely together that water couldn’t penetrate between, but you can put them so close that grout can’t get pressed into the gap sufficiently during the grouting process.
Compatibility
For rendering images, it is best to stick to standard gloss-finish or iridescent finish instead of mixing the two. For mixed media mosaics, a variety of finishes could be considered, but your mosaic might look better if you stuck to one or the other.
Cutting Elementile 8mm
This product cuts extremely well with the mosaic glass cutter that we sell. In fact, the homogeneous nature of pate de verre glass means that it cuts better than most types of glass tile and produces more useful pieces with fewer splinters and dust and waste.
Use in Mosaic Art
A set of tweezers can make working with these tiny tiles a lot less tedious. An 8mm Tile Mounting Grid is available for mounting designs one Mounting Paper or Tile Mounting Tape. For dry indoor mosaics, these tiles can be mounted with Weldbond Adhesive.
Elementile’s rich color palette make it a professional rendering tool that can be used for photo-realist portraiture and fine art mosaic. The colors available are more like the canonical hues of artist oil paint and less like the arbitrary mixed hues of most lines of architectural tile. The material cuts very cleanly into small pieces that can be used for micro-mosaic artwork.
How To Make Mosaics
For more advice on designing your mosaic project or cutting and grouting tile, please see our Mosaic Frequently Asked Questions page or our How To Mosaic blog or our Mosaic Information Guide.
; [product_table category=”elementile-iridescent-recycled-8mm” widths=”auto,auto,12,12,20″] ;